

For beautiful results with that machine, switch to solid wire and C25 gas (If it accepts gas.which I assume it does, as its call a 'MIG'). Single or multiple pass welding on up to 19 mm (3/4 in) thicknesses General fabrication Robotics Truck bodies, tanks, hoppers, racks and scaffolding Welding on galvanized steel or zinc coated carbon steel 104 THE LINCOLN ELECTRIC COMPANY Conformances AWS A5.29/A5.29M: 2005ASME SFA-A5. Thin sheet is tough, and you are not using the best tool by using flux core (it burns hotter than solid). You can walk around the joint with this method and end up with a fairly decent looking weld seam. A lot of your success will depend on watching the weld fade from bright red down.you have to let that very first color shift start before the next dot.it'll be less than a second apart for the spots. Once your dots (about four) are spaced around the joint you can go back to the first and begin doing dot-dot-dot-dot, each touching the last, pretty much like you see TIG welders do,but be sure you get that momentary sizzle each time. Start out with spots spaced opposite and spread around the tubing.do NOT try to do a continuous weld!. If you blow through.You were too close, too hot (check machine), or lingered too long.go for the briefest sizzle you can get.
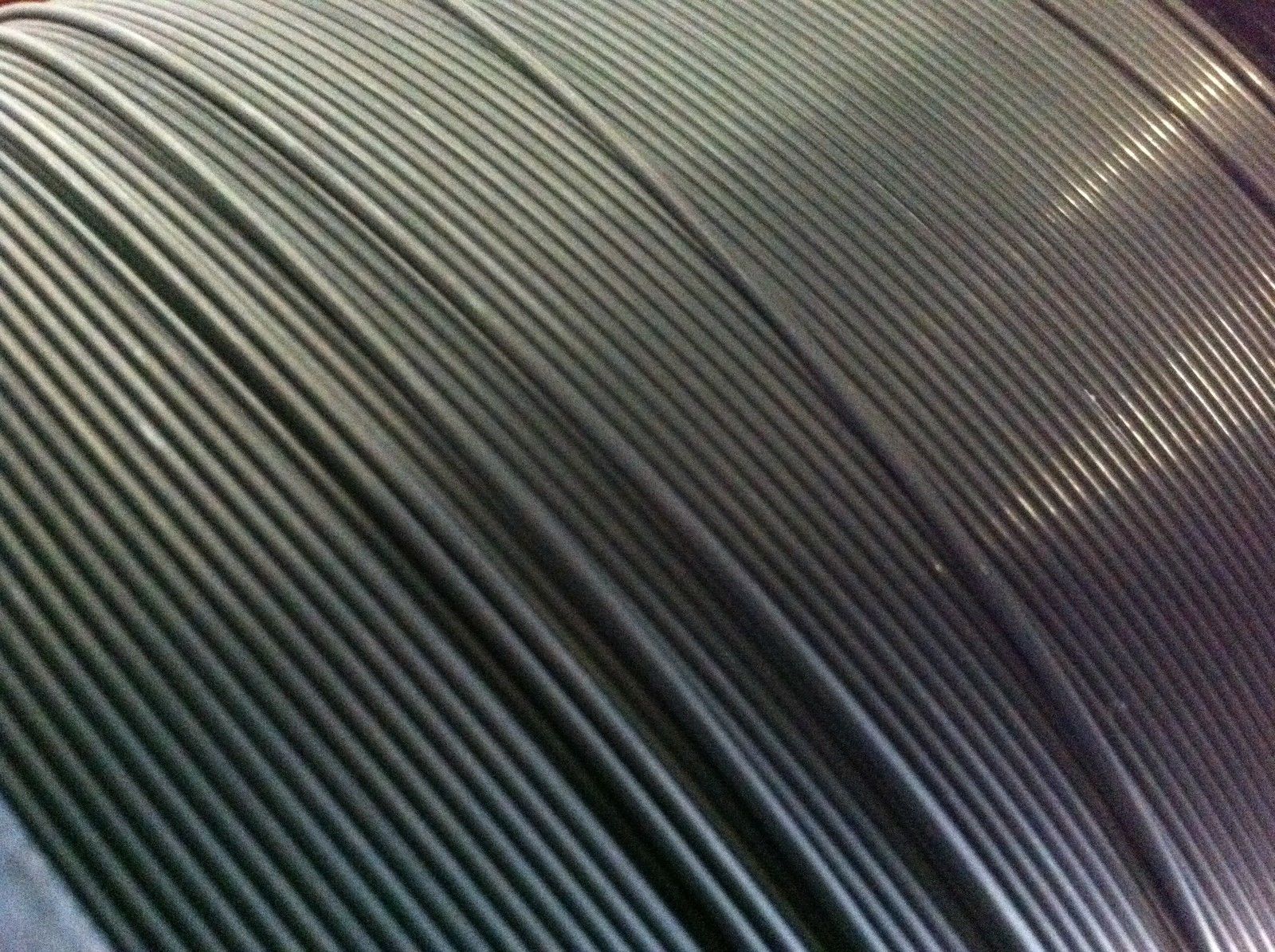
You need to get a weld, not simply a blob, so listen for the 'sizzle', brief as it might be (less than a second). I usually start out with about 5/16" stickout. The rusted requires structural assistance (Usually a plug of rebar tapped inside before welding), and those 'dots' just need to be re-done correctly.which means.ĭo not point your gun 'straight into' the weld, but, rather, tilt it back 20 degrees or so.ĭo not hold the nozzle too close to the weld. See my EMT framed Rocket Powered Wheelchair in the Metal Art section) I do weekly repairs and amendments to a fair amount of old Patio Furniture and Garden Items (plant stands, Bird Cages, etc.), most of which is badly rusted (was sitting on wet dirt), or had puny little 'dot' welds (I wouldn't even classify them as "spot" welds).and much of it is about the same wall thickness as EMT.

Well, Dave, you are not alone on your pathway into welding thin sheet steel (or EMT as the case might be)! Thin in very 'touchy', and is far better done with gas and solid do quite a bit of really thin, rusted tubing with my 125EZ using.
